Global vision, local action: Inside Schaeffler’s roadmap to climate neutrality across Asia Pacific.
We hear a lot about climate pledges at global summits. But real change? That’s built on plant floors, within supply chains, and in daily operational choices. At Schaeffler, sustainability isn’t just a future aspiration, it’s a process in motion. Various teams across the region are translating the group’s ambitious climate neutrality goal (covering Scope 1, 2, and 3 emissions) into tangible, locally-led progress.
Why It Works: Ownership Drives Action
“Sustainability isn’t a side project. It’s serves as our license to operate.”
This ethos drives Schaeffler’s approach across the region. Rather than top-down mandates, Schaeffler’s manufacturing plants in Asia Pacific are empowered to create their own decarbonisation playbooks.
Why?
Because a plant in Korea faces different energy challenges than one in India.
“We don’t just execute strategy. We help design it,” Hyungjin Seo, Manager Corporate Strategy Asia Pacific and Head of the Region Asia Pacific Sustainability network said.
This belief sits at the heart of Schaeffler in Asia Pacific’s Sustainability network, which plays an integral role in aligning global ambitions with local realities.
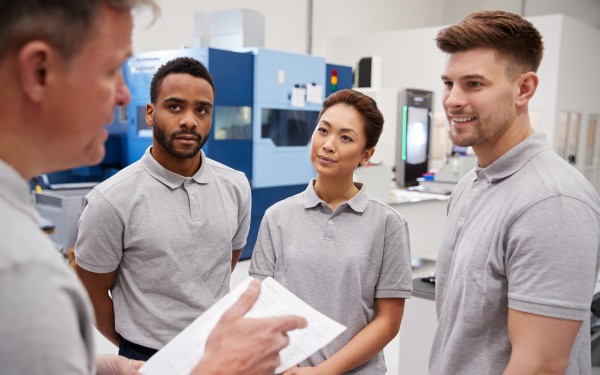
Drawing on insights across Corporate Strategy, Operations, Purchasing, Research & Development, Human Resources, and Schaeffler’s business divisions, the network serves as a regional platform for steering sustainability priorities, driving cross-functional collaboration, and shaping initiatives that deliver measurable impact.
Schaeffler’s climate transition plan outlines key levers across the business. In Asia Pacific, that includes the use of energy and carbon monitoring systems, implementing energy efficiency projects, and a shift toward renewables. These efforts are guided by science-based targets and embedded in daily operations.
This decentralised approach turns intent into impact. With autonomy to lead and accountability to perform, each site becomes an active agent of sustainability.
How Targets Take Shape
At the core of Schaeffler’s strategy is continuous optimisation. That means every part of energy usage, from sourcing to consumption to monitoring, is viewed as part of one integrated system.
In its manufacturing sites in South Korea, solar panels are installed for self-generation, supplying power to be used in production processes. Likewise, Schaeffler’s manufacturing plants India are installed with digital energy meters to identify inefficiencies in real time. In Vietnam, smart dashboards help teams adjust performance before spikes happen, showing measurable year-on-year improvements in energy consumption and emissions.
“We’ve moved from spreadsheets to smart systems,” shared Thomas Berthold, Head of Sustainable Production Asia Pacific. “Now, saving energy is not just good practice. It’s how we work.”
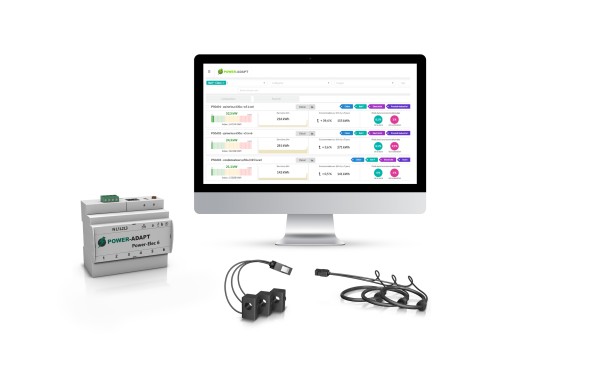
Flexibility Fuels Progress
Every location is different. That’s why Schaeffler doesn’t rely on a single energy model. Instead, sites adopt a flexible, multi-path energy strategy; one that combines green tariffs, power purchase agreements (PPAs), and Energy Attribute Certificates (EACs) depending on local infrastructure and market maturity.
In some markets, that means partnering with energy providers through long-term PPAs to secure stable, renewable supply. In others, where renewable grid access is limited, sites are supplementing with EACs or investing in onsite renewables as conditions allow. The approach is not only about decarbonising quickly but doing so in a way that supports business continuity and operational resilience.
Additionally, this modular strategy gives each site a practical starting point while staying aligned with the company’s long-term sustainability targets. It also allows Schaeffler to adapt in real time as energy regulations shift, technologies evolve, and renewable access improves—transforming global ambition into local execution.
The Factory Floor is Where Change Happens
In Asia Pacific, decarbonisation begins on the production floor. Across various manufacturing sites, production lines are being redesigned to slash idle energy. Heat recovery systems are in pilot, and designs for lighting automation systems are currently underway.
But the most powerful shift isn’t the hardware - it’s the mindset.
Energy efficiency has moved from being a standalone initiative to becoming a shared performance metric. Sustainability KPIs are now embedded in productivity dashboards, aligning environmental outcomes with team objectives.
Digitalisation turns intention into impact, where real-time monitoring tools spot anomalies, sensors optimise performance, and teams share wins. These may appear incremental, but they are the foundations of scalable transformation.
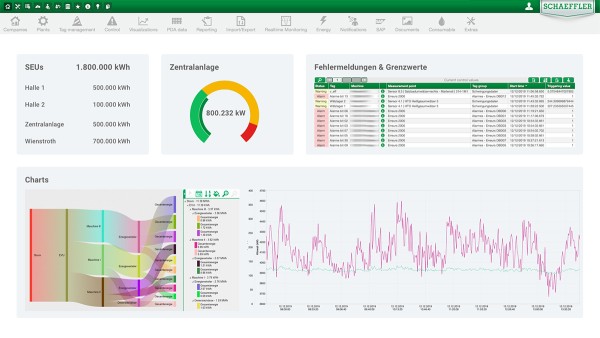
Leading by Example
While global conversations around decarbonisation often remain at a high level, Schaeffler has prioritised implementation. A digital energy tracking pilot has grown into a regional blueprint, empowering local sites to take ownership of their data and results.
Local champions, from shopfloor engineers to maintenance leads, are stepping forward to lead the shift towards sustainability. Whether it’s through cross-functional task forces or targeted upskilling in energy efficiency, teams are taking ownership in meaningful ways. What began as a test is now the standard. And each success builds confidence for the next.
Progress Without Greenwashing
With varied regulatory environments and infrastructure across Asia Pacific, the company prefers to stay grounded. But results are emerging. Sites are reporting measurable gains in energy intensity, and systems for tracking, validating, and reporting emissions are growing more robust every year. It’s not about big headlines. It’s about building credible, visible progress with integrity.
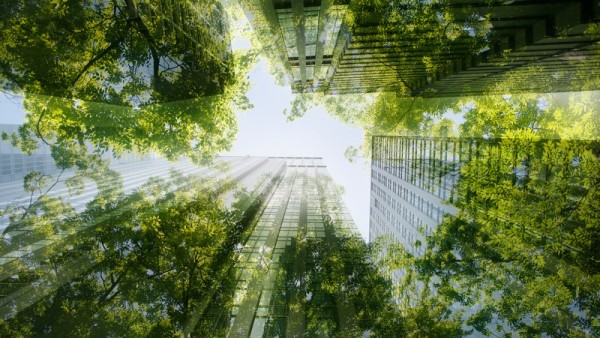
Shaping the Future of Sustainability Together
Schaeffler’s mission extends beyond its own footprint. As a leading motion technology company, it plays an active role in the decarbonisation of entire industries, assuming responsibility in making the machines, vehicles, and supply chains of tomorrow, more climate-friendly by design.
Our shared journey for a better tomorrow isn’t linear, but momentum is clear. With local ownership, smart technology, and an unwavering focus, the company isn’t just planning a sustainable future — It’s engineering it into motion.